What is OEM Die Casting?
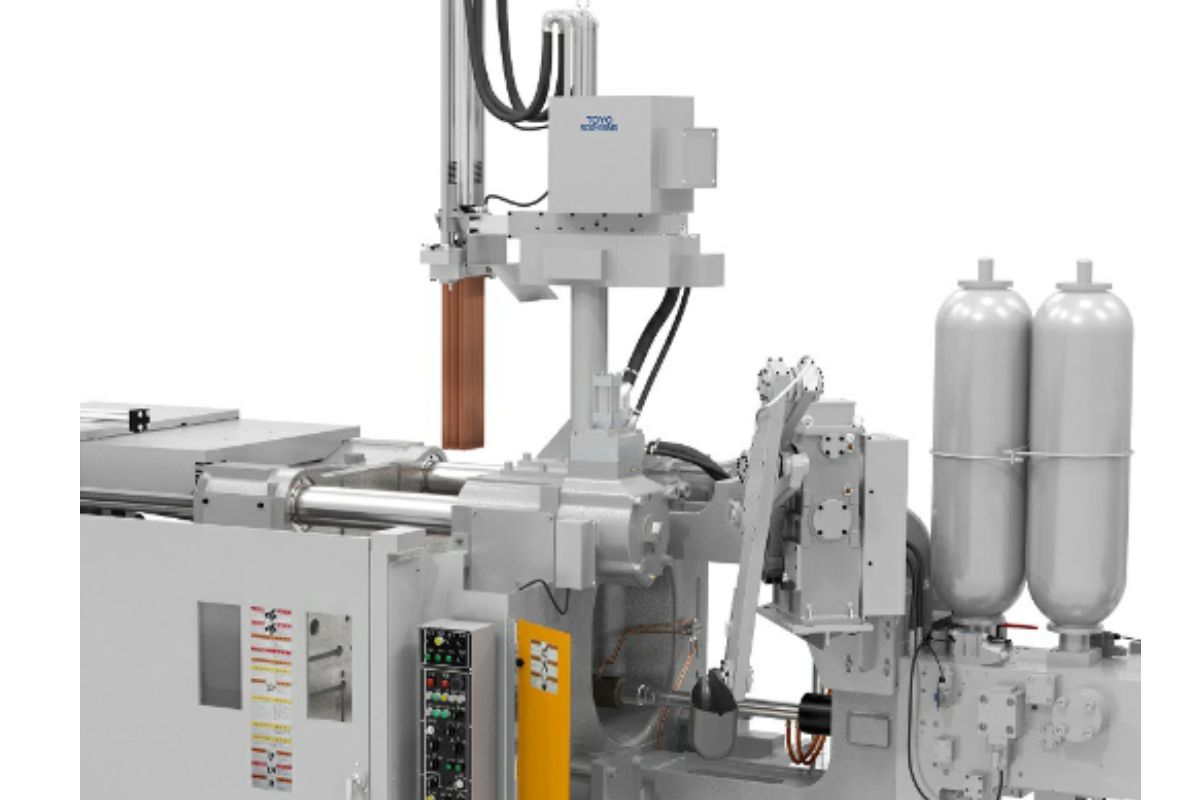
Die casting is a manufacturing process used to create molds for making metal parts. It’s a cheap and efficient way to produce parts. Die casting is used in industries that require a high output of parts. It can be used for manufacturing small or large items.
Die casting is not just limited to small items. Die casting is a technique that can produce molds for creating parts that are larger than life. For example, die castings for automobiles, boats, garden furniture, lawnmowers, and food processing machinery are some of the items that are produced using this process.
But that’s not all! With the right knowledge and skills, you can also start a business casting parts at home. Read on to discover more.
What is Die Casting?
Die casting is a casting technique that involves metal being heated to a temperature higher than its melting point, turned into a sludgy liquid, and then poured into a mold, is an ancient metalworking technique. It has a long history, dating back to the Mesopotamian civilization around 3600 B.C. when bronze was processed.
Since then, casting using molds has evolved with the development of technology, giving birth to dying casting technology that can produce beautiful casting surfaces, high dimensional accuracy, and the possibility to manufacture thin-walled, complicatedly shaped castings in a short amount of time with high cycle durations.
Die Casting Process
Die casting is a mass-production casting method in which molten metal is injected into a precision mold at fast speed and high pressure to fill even thin-walled sections. Die casting is divided into two processes: standard die casting and new die casting.
Standard Die Casting Method
Die casting is a mechanism that injects molten metal into a mold at high pressure, and the die casting equipment, which is called a die casting machine, is quite massive in order to ensure the clamping force to withstand the high pressure. Die casting machines are divided into two categories: cold chamber die casting machines and hot chamber die casting machines.
(1) In a cold chamber, molten metal poured into a sleeve is pressurized and injected into the mold by a plunger. This process is used to make all aluminum alloy die castings. It is also utilized in the production of magnesium alloys and brass.
(2) In the hot chamber type, the sleeve and plunger are immersed in molten metal, which is then pressured and cast into the mold through the gooseneck. This process is used to make the majority of zinc alloy die castings. Magnesium alloys are also produced with it. Because the molten metal erodes the sleeve and plunger, this method is difficult to apply to aluminum alloys, although it is currently being developed for small machines.
The die casting process steps
Mold release agent application
A water-soluble mold release agent is applied to prevent seizure and reduce extrusion resistance during mold release.
Clamping the mold and supplying hot water
The clamping force moves the movable mold to close the mold, and a ladle pours molten material (molten metal) heated above melting temperature into the mold.
Injection (molten metal filling)
The plunger applies strong pressure to the molten metal in the mold and pushes it into the mold to fill it.
Mold opening and product extrusion
When the molten metal cools and hardens, it transforms into a “casting” with the mold’s shape transferred. An ejector pin is used to force the castings out of the mold, and any unneeded components are removed to complete the product. The cycle continues by returning to the process of step 1 ; applying mold release agent.
New Die Casting Methods
Due to high-speed injection filling, it is difficult to eliminate air and gas entrapment in thick-walled parts when employing the standard die casting process. To improve fillability, tightness, and mechanical qualities, as well as heat treatment and welding, new die casting methods have been developed.
Vacuum die casting process
To minimize pressure, air and gasses in the mold cavity are sucked out with a vacuum pump right before molten metal injection. This method requires ingenuity in terms of maintaining vacuum and managing molten metal injection timing.
There are numerous approaches, including the gas free (GF) method, mass vent method, cutoff pin method, and VACURAL method, depending on the method. An air vent valve is used to quickly remove a large volume of air from the mold cavity while also preventing molten metal from escaping to the outside. The VACURAL method involves depressurizing the inside of the sleeve as well as suctioning the flowing metal to speed up the depressurization process. Welding and solution heat treatment are both possible.
PF die casting process (pore free die casting process)
The molten metal is cast atomically into the mold at a high injection speed of roughly 80 m/second or higher, spreading all the oxygen as Al2O2 into the castings to eliminate casting porosity caused by air and gas entrapment. The gas content is comparable to that of the normal/gravity die casting method, and solution heat treatment and welding are both possible.
Low-speed filling die casting method
Molten metal goes through the gate at a modest speed of roughly 1 m/sec to prevent air and gas entrapment in the sleeve and mold cavity caused by high-speed filling.
The accurad method, low-speed filling method, and laminar flow filling method have all been developed. Because of the extended filling period, it’s critical to increase the gate cross-sectional area and keep the molten metal from cooling too quickly. It is possible to cast sturdy and pressure-resistant pieces.
High-Speed Fill Die Casting Method
Aluminum alloys require the casting of thin-walled items with a wall thickness of about 0.8 mm. As a result, the use of high-speed filling with a gate passage speed of 80 m/sec or greater, rather than low-speed filling, has recently gained traction. The plunger travel speed and stop mechanism must be precisely controlled.
Localized pressurization method
A time lag is supplied after filling the molten metal to suppress the production of porosity in thick-walled portions far from the gate, and a local pressure pin is applied to the thick-walled section in a semi-solid condition to push it in and pressurize it to crush the porosity-generating area. It’s also used in high-pressure casting methods.
Die Casting Benefits
Mass production of products with complicated shapes
Die casting has the advantage of giving greater freedom when molding, compared to sheet metal. Molds with higher precision allow manufacturers to create products with more complicated shapes. Complex shapes, such as three-dimensional shapes, that are difficult to make with sheet metal can also be manufactured.
The die casting process also has the advantage of being able to perform continuous casting in a few tens of seconds. In a short amount of time, large volumes of products can be manufactured. The yield rate is very high, allowing for minimal manufacturing costs.
Good dimensional accuracy
The die casting process is a dimensionally accurate casting method. The oem die casting has a high level of dimensional accuracy, ranging from 6 to 7, with a maximum of 4. Even if a product’s shape is complex, it can be precisely cast to a certain dimension. Machining may not be required if the surface can be made smooth. Significant cost savings can be achieved if secondary machining is not necessary.
Good product quality and recyclability
It has a good surface finish, usually ranging from 5-8. High strength and hardness, often 25–30% higher than sand casting. However, with extension, speed is reduced by around 70%. Sizes are replaceable and stable.
Higher precision improves the product’s strength. Because no further processing is necessary, defects are less likely to occur, and materials can be reused even if a mistake is made because they are highly recyclable.
Die casting’s excellent recyclability may make it an appealing technology for environmentally conscious companies. When using inserts, manufacturers do not have to choose metal, and because aluminum alloys have a low melting temperature, the molds have a longer life. Manufacturers don’t have to choose a metal when using inserts, and the molds last longer because aluminum alloys have a low melting temperature.
Contributes to thin-wall weight reduction
Die casting can produce thin-walled, lightweight items with complex shapes. Die casting can be used to create complex castings with thin walls. Current zinc alloy die castings, for example, have a minimum wall thickness of 0.3 mm.
The minimum casting hole diameter is 0.7 mm, and the minimum pitch is 0.75 mm for aluminum alloy castings up to 0.5 mm. Oem die casting is widely utilized in the automobile sector, industrial machinery, electrical equipment, telecommunications equipment, precision equipment, and other fields where parts must be lightweight. Lightweight parts are presently being manufactured in the automotive industry because the lighter the part, the better the fuel efficiency.
Die Casting Disadvantages
- Heat treatment cannot be used to reduce the porosity of the die-cast item. Die casting has two key characteristics: high pressure and high speed filling.
- The initial investment is pretty substantial. Before mass production can begin, molds must be purchased. Molds, which are required for oem die casting, are quite expensive.
- Die casting defects in products increased significantly throughout time due to short die casting life, alloys with high melting points (copper, ferrous metals, etc.), and OEM die casting defects in products with high melting points (copper, ferrous metals, etc.).
- This product is not appropriate for small-scale manufacturing. The main reasons for this are that OEM die casting is an expensive process to manufacture, die casting machines have high production efficiency, and small-batch manufacturing is uneconomical.
Conclusion
Die casting is extensively utilized for mass-produced equipment and housings because of its exceptionally high dimensional accuracy and ability to be created at a fast speed if a die is available. However, the benefits of oem die casting outweigh the costs. Therefore, weigh the costs of die casting vs. alternative manufacturing methods to see if die casting is the best option for your production volume.